Selection of a product component for topology optimization and additive manufacturing
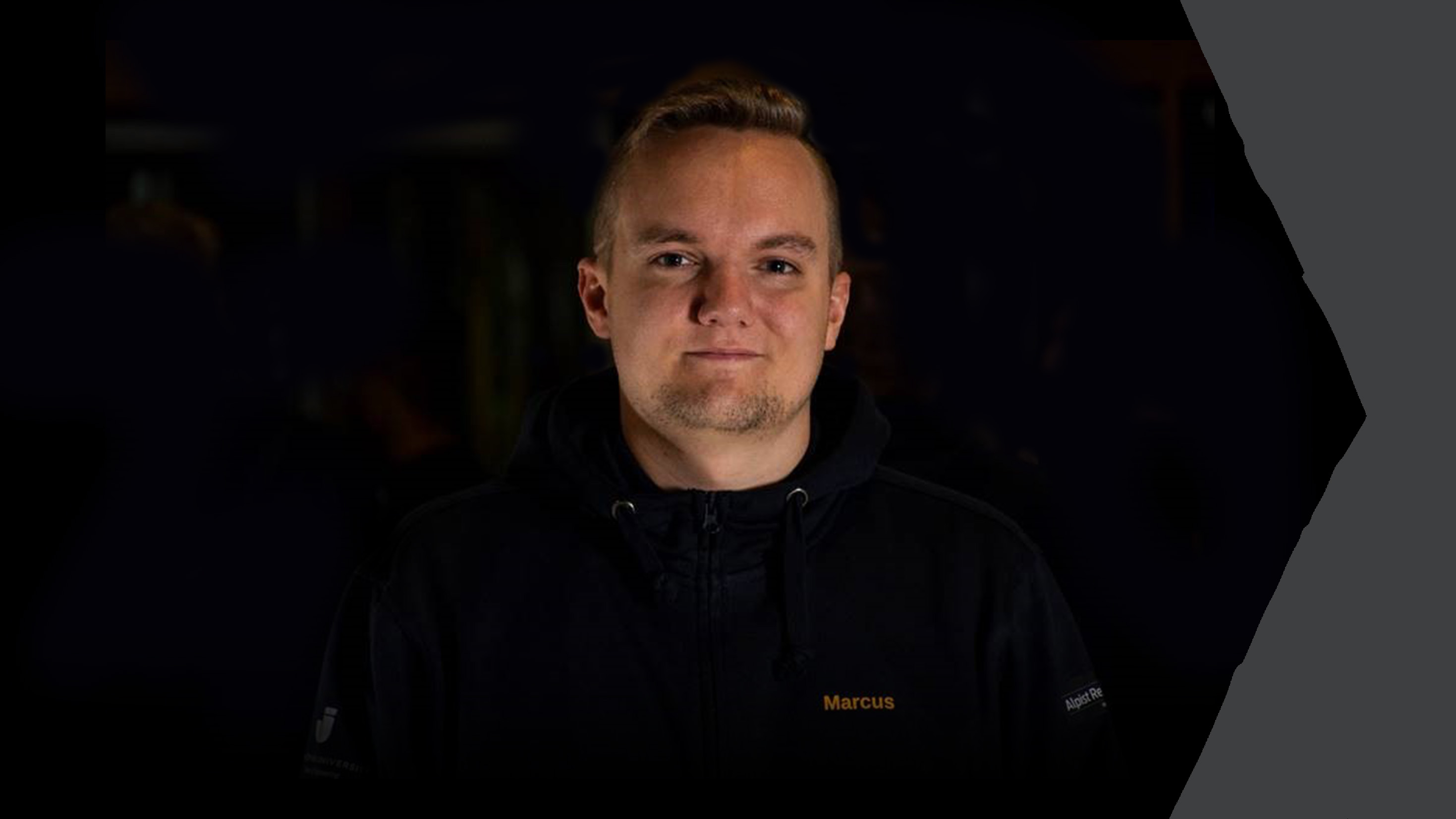
Product Development and Materials Engineering
Marcus Svensson
LinkedIn Länk till annan webbplats, öppnas i nytt fönster.
The research tackles the problem for how to select the right components in a product, considering reducing the weight with topology optimization (TO) and adaption for additive manufacturing (AM). At an early concept and development stage, with a methodology workflow.
It is well established that manufacturing of complex structures can be achieved with AM, the possibility of integrating assembled components and improve features is therefore investigated. The new component structure must still withstand the loads that it is subjected to during usage, to not permanently deform or break.
In this research the case studied product was a handheld Husqvarna chainsaw. Reducing both the weight and the number of assembled components can have benefits for both the user and the company. It could lead to minimizing fatigue and injuries from the different static operating positions that the customer is challenged for every day at work, but also improve the user experience. A positive effect with the usage of AM could be the reduction of used material, which also could lead to improved environmental sustainability. Due to potentially reduced resources and energy during the products life cycle, with a redesigned lightweight component.
Initially a feasibility study was conducted, where the product was disassembled and physically investigated for potential component cases. Additional knowledge was gathered with semi structured interviews with experienced design engineers and AM experts, regarding available AM technique and similar material. Selection of case to continue with was based on the interviews information and a decision matrix, with weighted criterions. TO was used for finding the optimal material distribution. The new component design was analyzed with linear finite element analysis to fulfill both the component and material stress requirements. The simulation took into account the engine speed range for different load cases with linear static structural analysis, dynamic eigenfrequencies and frequency stress response analysis. Component orientation and support structure for AM was analyzed and reduced with computer aided engineering software.
This resulted with integrating thirteen components for the engines cylinder into one component. The new design resulted in a weight reduction of 31%, while utilizing only 57% of the allowed stress limit. Also, the first 23 natural frequencies were improved with a new type of cooling fin structure, with an increased cooling area of 15%. These results encourage the thesis workflow methodology to be used on other products as well. In conclusion the established workflow of methods resulted in selecting a suitable case for integrating components with possible feature improvement and adaption of the new design with TO for AM, in order to reduce the weight and used resources.