Sometimes it is not technology!!!
In 2015 we decided to hop on the additive manufacturing train. Additive manufacturing had been a buzzword for some time. Above all, it is a paradigm change for manufacturing. Not today, but tomorrow!
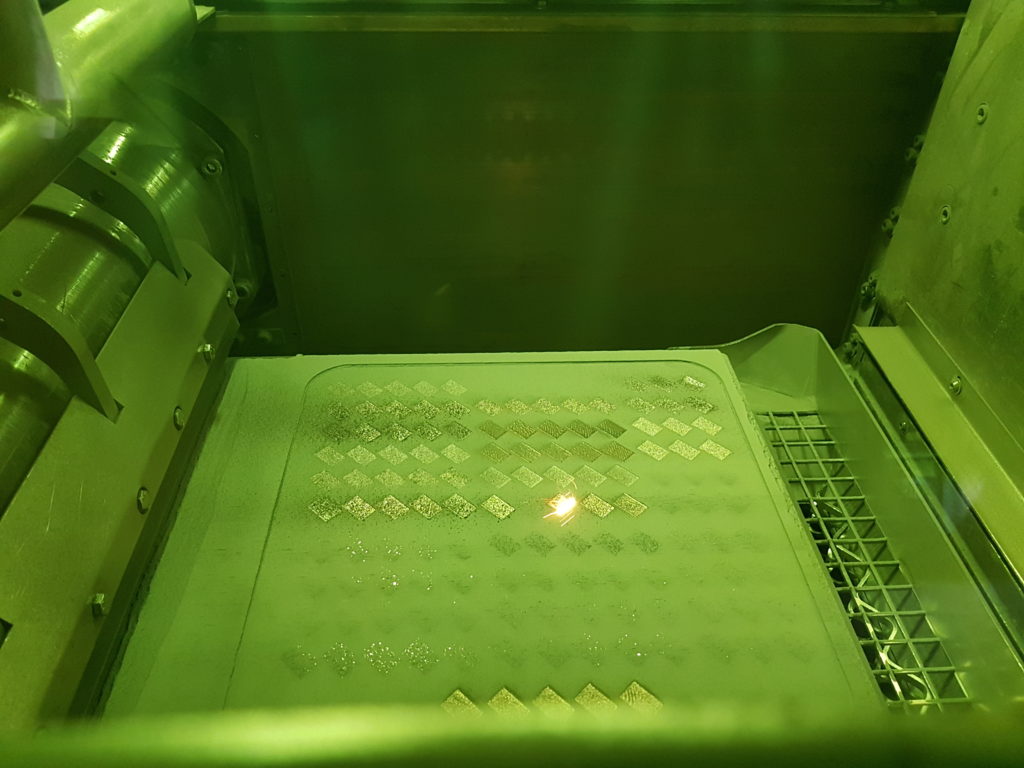
What are the drivers?
Before starting the additive manufacturing initiative, we had a workshop, with the potential partners. We found that the main drivers for our industrial partners were:
- Stronger individualization of products and services, more customization
- Lighter, sustainable, and “first production hit right” manufacturing tools and dies/components/products
- Strongly reduced environmental impact in manufacturing processes
- Higher productivity in BOTH engineering and production
- Shorter lead times (including short Time To Market (TTM) and short Time To Production (TTP))
- A stronger focus on integrated virtual product and production development
- Increased production flexibility (both volume and variant)
- Reasonable manufacturing costs
Although cost has been argued for a long time, Time To Market and Time To Production were the real winners! So actual lead time is truly important! This we took as a target. Our ambition became to use additive manufacturing for tooling manufacture!
Together, the departments of Materials and Manufacturing and Product Design and Development have a strong portfolio in tool making and design. Related to additive manufacturing we have had 6 projects. The tooling design with modularisation, adaptation to additive manufacturing and understanding design for maintenance, and shorter time to the user all targets shorter Time To Market and shorter Time To Production.
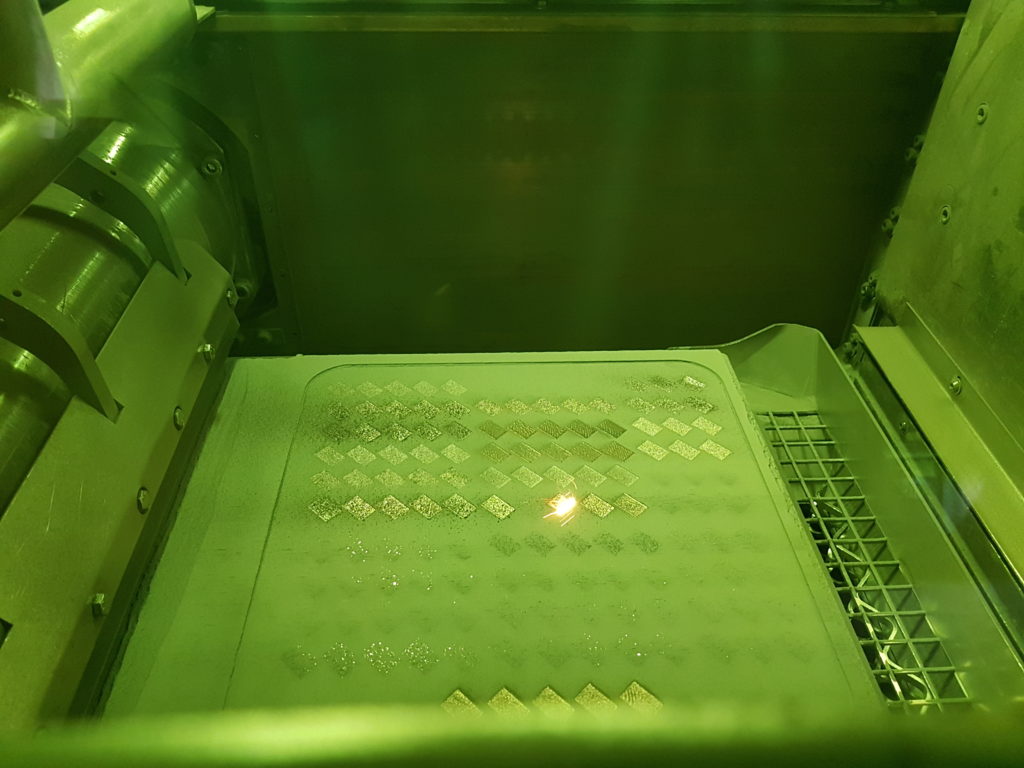
Additive Manufacturing @ JU!
We are nowadays working on tooling design and to print this is both conventional AM materials and also to help to introduce new AM materials for toolings. We are now starting to print insert to be used in our own research project. The synergy between project will be to validate these new materials. Topological tool design will allow processes such a high pressure die casting to create thermally stable tools. Moreover, this will improve tolerance management, tool life and productivity. This will truly be an engineering and technology paradigm change. faster more efficient and reduced cost of ownership
But what about the Time To Production
Today a casting tool in Sweden takes roughly 20 weeks to get to the foundry. Subsequently, the process needs trimming to produce good parts. Additive manufacturing will naturally reduce this time. Our ambitions were perfect…….until I med Edward Zhao.
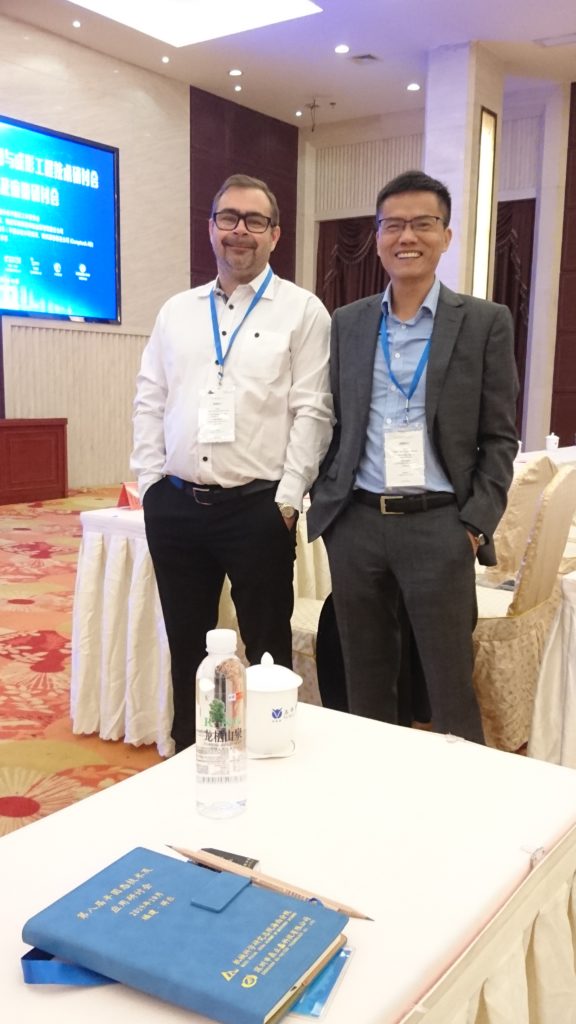
it is not all about technology!
Edward Zhao with RheoComp Technologies told me that in China it takes 5 weeks to get the product to the customer including tool manufacturing and trim the process. This without the additive manufacturing. Additive manufacturing would cut another week and create an even greater advantage.
The only explanation for this huge advantage is only due to that there is free capacity with the toolmakers and heat treaters and so forth. The real question here is thus if our chase for efficiency has struck back? Perhaps it is also about slack!
So sometimes it is not about technology!
What to do now?
The real gain here is not only related to the change of technology but also the mindset and working principle. Resource-efficient manufacture and tolerance management in tools for casting will increase capability. This will increase process yield and reduce energy usage, reduce the carbon footprint for production. Additive manufacturing will for many products be the way forward but not alone. We need to take a look at the whole manufacturing eco-system adapt, adopt and move faster and smarter….and perhaps allow us some slack!
Detta är en bloggtext. Det är skribenten som står för åsikterna som förs fram i texten, inte Jönköping University.