Additve manufacturing for the die casting toolmaker
Additive manufacturing is often seen as the new manufacturing method. This may very well be the case as well. One of the areas of early adaptation is tool making, which has worked well for polymer injection moulding. The introduction of additive manufacturing into high-pressure-die casting has taken time. This has many reasons, some are explored in this blog post
What drives the use of additive manufacturing in toolmaking for high-pressure die-casting?
In polymer injection moulding, the cycle time is dominated by the time it takes for the polymer to cool and solidify. Typically for a cycle time of 1 minute, this time is 20 seconds. Conformal cooling dies, dies with cooling channels near the die cavity, can dramatically reduce this timing, shortening the cycle time. In a casting process with a cycle time of 1 minute, the solidification time is less than 5 seconds. The solidification time is not the limiting case for conformal cooling, nor can you gain significant cycle time by reducing the time to solidify. Other gains must be sought to reap benefits from additive manufacturing in high-pressure die-casting. This also means that what we have learnt from the polymer injection moulding experience with additive manufacturing needs to be unlearned. New knowledge must be replaced with appropriate experience.
Relearning the actual value of additive manufacturing for high-pressure die-casting
In high-pressure die-casting toolings, the main driving cost is die-life. In aluminium high-pressure die-casting, the expected die life is 100000 shots, and the dream is 500000 shots. It should be noted that this is for the main die cavity, and other tool parts, such as core pins and such with a heavy thermal load, may need earlier replacements. Die wear causes process interruptions as die sticking and flash are formed, disturbing the process and causing process losses from start-up cycles after interruptions and productivity losses. So far, the only weapon against this has been die spray intensity to reduce the temperature in hot regions. Increasing die spray will inherently reduce part quality as die spray drives porosity generation. A new approach is required!
Increasing die life
The primary purpose of any cooling solution should allow for a lower surface temperature. This would suggest that one route for increased die life. The best way to improve die-life is to reduce die temperature. A reduced die temperature will affect the fluidity and fillability of the metal over large surfaces driven by the significant temperature difference between metal and die, which is not present in polymer injection moulding. This means that local heat management for sensitive parts is one approach.
Local thermal management of core pins is one of the most successful adaptations in casting where direct learning from injection moulding could be made. This is also where some applications are seen. This will increase the service intervals and reduce the interruptions in the process, reducing the associated costs, but will not significantly affect the die life.
Another way to reduce the die's thermal load is to use semisolid metal slurries in high-pressure die-casting. It has been shown that using semisolid casting, 400000 shots can be realised in production. This suggests that a possible route forward combines additive manufactured toolings and semisolid processing for high-pressure die-casting.
A better understanding of what is happening in the die.
Ina recent study, the effects of conformal cooling were investigated, including a comparison between conventional high-pressure die-casting and high-pressure die-casting using a semisolid slurry.
The comparison was with and without conformal cooling in conventional and semisolid high-pressure die-casting. The conformal cooling insert is shown in the figure.
First, conformal cooling was effective and could increase the die's cooling rates by a factor of three based on oil temperature and flow rates in the die tempering systems. This means that the cooling channels worked as expected. For semisolid processed material carrying less heat into the die, it was difficult to fill the die and the die's set-point of the die heating system needed to be maximised. This implies that conformal cooling in thin-walled castings and semisolid processing may be counter-productive, suggesting that conformal cooling of the main cavity may be of questionable use and that other possibilities should be explored.
A rather unexpected matter was also found for the semisolid processing. As the melt viscosity is more than 1000 times higher, the pressure at the entrance is much higher, leading to good contact between the melt and the die at the entrance making the entry point hotter for semisolid metal processing than for conventional processing. This means that the thermal stress at the entry point is higher for semisolid materials than for conventionally processed materials. This is, however, not true for the rest of the cavity. Semisolid processing generally increases die life but not for parts of the die.
What to do, then?
The key to success is the effort to reach a cost-effective, carefree, high-pressure die-casting die life. To reach 500000 shots in a die thermal load, die surface temperature needs to be minimised. Choosing not to work with die-spray is detrimental to part quality. There are only three things to do.
1) Reduce the heat entering the die, meaning that it is essential to use semisolid casting, despite the drawback of a hot entry point.
2) Start using additive manufacturing for core pins to allow fewer service intervals
3) Find other routes to use additive manufacturing than to create conformal cooling channels in a die cavity, as these are ineffective in reaching the goal.
The other routes mean that instead of cooling the main die cavity, additive manufacturing should be used to control warping and tolerances in the die cavity. Step number one is to take the heat from the melt entry point at the sprue bushing and move that heat not away from the die but to other areas to reduce warping. Step number 2 is to ensure the right stiffness and to remove mass from the toolings with the same target to control the warping of the die. This approach, combined with the idea of puzzle dies to reduce stress in the die and to increase serviceability in the die systems, is a route forward.
If you want to know more!
Jarfors, A.E.W.; Sevastopol, R.; Seshendra, K.; Zhang, Q.; Steggo, J.; Stolt, R. On the Use of Conformal Cooling in High-Pressure Die-Casting and Semisolid Casting. Technologies
2021, 9, 39.
https://doi.org/10.3390/technologies9020039 External link, opens in new window.
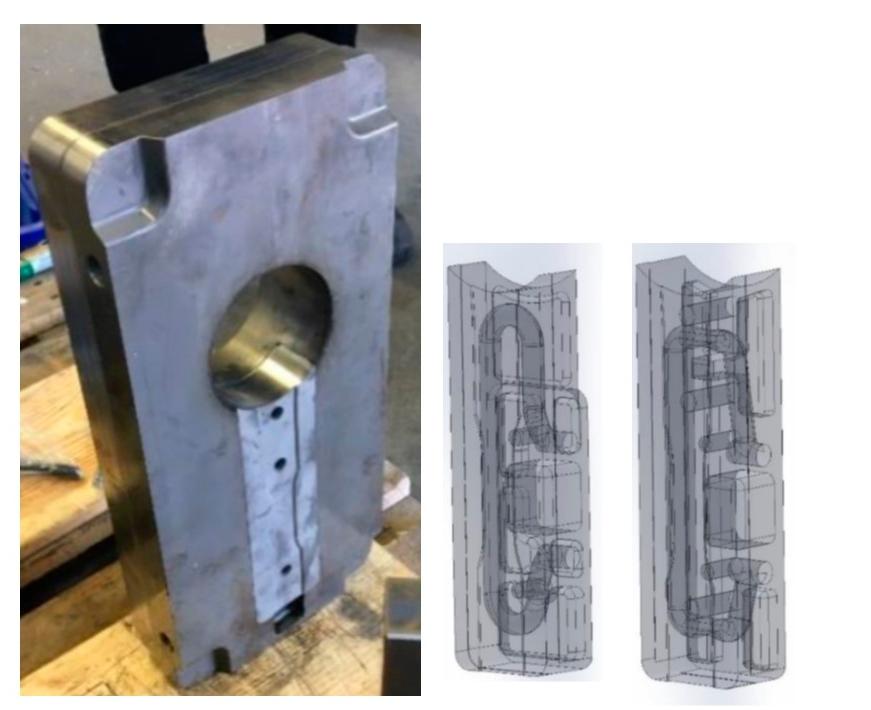
Conformal cooling die and the channels visualised
Detta är en bloggtext. Det är skribenten som står för åsikterna som förs fram i texten, inte Jönköping University.